In Newport-on-Tay in Fife, Scotland, Elaine and Tom Devine were happy in their Victorian house with its spectacular views of the River Tay. However, as they were approaching retirement, they realised the house wasn’t going to be practical forever.
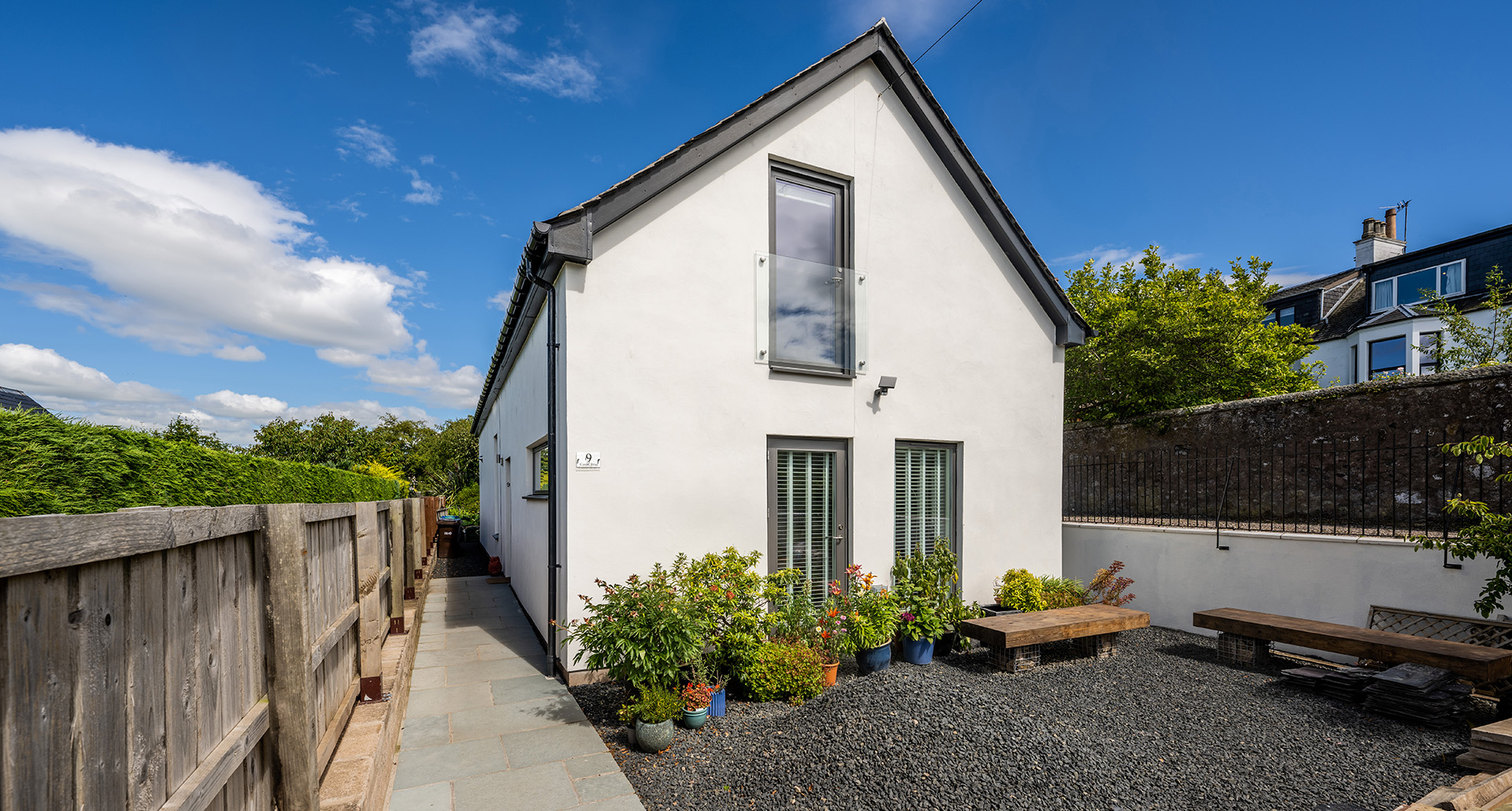
The idea to build a house on their land came after a neighbour built on theirs. “I watched that go up and remember thinking ‘I wonder if we could squeeze another house onto our plot’,” Elaine says. But as it was narrow, she “kept thinking it just wouldn’t work.”
Tom and Elaine’s main requirement for the house was for it to support their needs the rest of their lives; as opposed to their old house, which was “full of stairs.” They consequently had a goal from the outset for the downstairs to contain a living room, kitchen, bedroom, and bathroom.
They also didn’t want the upstairs space to be wasted as a loft, so included further bedrooms and a bathroom, which they use currently.
Their only other specific ‘ask’ was for a sunny, triple aspect living room. “Other than that, I was pretty open,” Elaine says. Part of her previous job role as an environmental health officer meant she saw a lot of people who ended up with unsuitable housing as their needs increased, so they also included wide doors throughout for a wheelchair, if necessary, in future. Another part of this ‘futureproofing’ was making the home well insulated and easy to maintain, which meant forgoing dust-gathering radiators and opting for underfloor heating.
In 2012 they approached Alistair Graham of Gillespie & Scott Architects, a firm that Elaine felt really understood the self-build market. Alistair prepared plans for a three-bedroom house to submit for planning approval.
Hands On
Because the couple were going to be hands-on with many aspects of the project, Tom wanted the building to be wind and watertight quickly, so they opted for a timber frame kit.
They came across Scotframe at one of the Homebuilding & Renovating shows and were particularly impressed by the company’s closed panel system into which the insulation is injected, including in the roof cassette.
“Because the site is very narrow, a standard off-the-peg kit wouldn’t have worked for us, said Elaine. “One of the reasons for choosing Scotframe was that they were able to work with our architect to create a bespoke solution tailored to our design.”
Tom had worked as a slater and roughcaster, so knew about working on sites, dabbling in various trades. While he did a lot of the physical work, Elaine took on the project manager role, as well as labouring wherever she could. While Tom had much of the practical experience required, Elaine’s former job had involved working with architects, so she understood a lot of the terminology, and knew how to decipher plans. “We made a good team,” she says.
They began work in 2018, sorting out the garden – half of which would be for their current house and half for the new house. The work included filling in a large pond and removing around 100 tonnes of soil. By March 2019, they had cleared and demolished the garage, before beginning digging out for the groundworks and foundations in July. They did all this themselves, as well as wheelbarrowing in all the aggregate and sand – necessary because the narrow site meant they couldn’t get the digger round the back of the site. “One of Tom’s best purchases were car ramps so we could take the digger over the trenches dug for the foundations,” says Elaine.
To save on cost, they bought the digger as well as the scaffolding (which Tom was able to erect himself) rather than hiring them. As a bonus, they sold them on for virtually the same as the purchase price at the end of the project.
The foundations were dug and the site was prepped, including the subfloor slab, by Christmas 2019. It was then a case of waiting for the Scotframe kit to arrive, which it did just in time – exactly three weeks before the first Covid lockdown in March 2020. “We had everything we needed, absolutely no shortages or delays in getting all the necessary materials to the site — Scotframe supplied absolutely everything we needed so we were able to get to work without any hold-ups. Tom knew a joiner, and we got a crane.
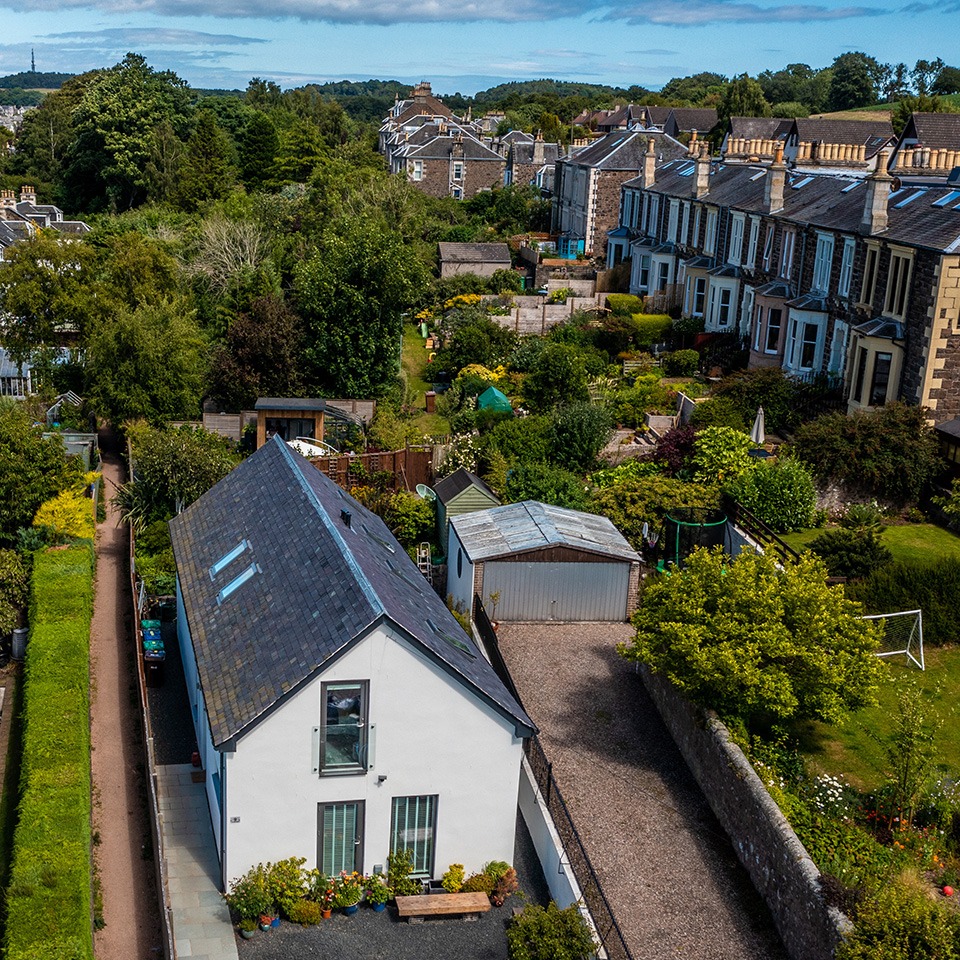
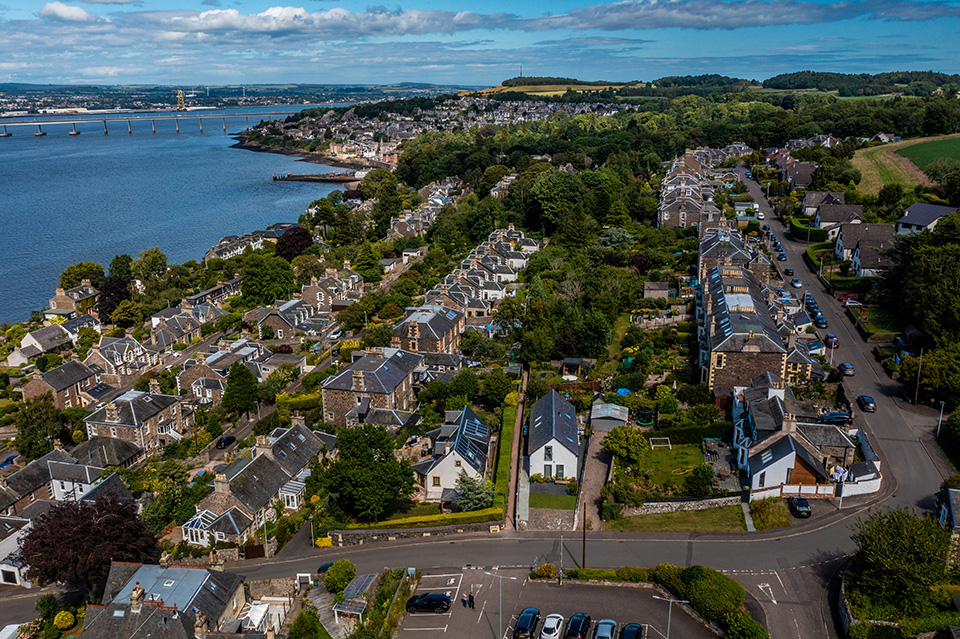
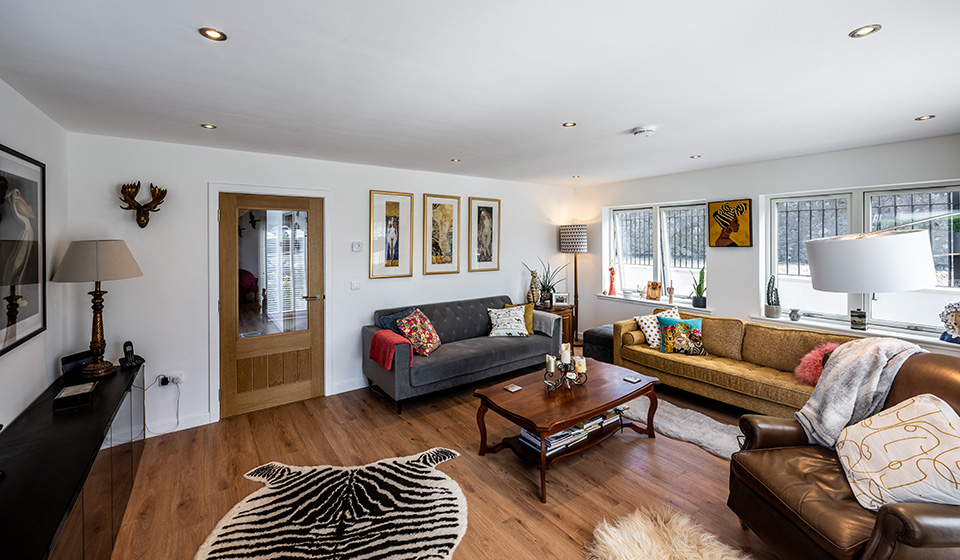
“We wanted our house to be air and watertight quickly. With Scotframe’s closed panels and roof cassettes, we achieved this — the construction went ahead really quickly; the roof was up in about three hours. It was a great feeling coming back to site one day to find four walls and a roof where there had been nothing, and you had just been looking at a piece of paper for years.”
Although looking to keep costs low, Elaine says they didn’t skimp on important things. “We got good quality, low maintenance triple glazed windows and oak stairs,” she says. “We spent money where we felt we needed to.” They were also able to be cost effective; the kitchen is from IKEA, and they chose laminate flooring over the underfloor heating downstairs, with tiles in the bathrooms. By this point Elaine said she was struggling to make decisions, and figured laminate would be easier to replace if she changed her mind.
Planning: if at first you don’t succeed…
The couple were open to ideas, especially knowing the narrow site meant their design would be constrained. The first design was an ‘upside down’ house to make the most of the river views. It was recommended by the planners for approval, and only two objections were submitted. The rules in Scotland dictate that if there are fewer than six complaints, the planning officer can proceed with the application. However, the community council lodged an objection, meaning the application automatically went to committee and was refused (in January 2013).
Subsequently, the couple worked with the same architect on a redesign, abandoning the upside-down concept. Once again, the planners were happy but the same two neighbours objected. To move things forward Elaine wrote a letter to every single member of the planning committee lobbying for approval. However, again the community council lodged an objection on the final day, and again it went to committee in January 2018. This time however, one councillor – holding Elaine’s letter – put forward a motion for approval, meaning it went to a vote, approved by eight to six. That personal touch, believes Elaine, seemed to make the difference.
Sustainability
Throughout the project, Elaine and Tom were conscious of being as sustainable as possible. As well as the timber frame, they reused all the material from a garage they had demolished, as well as buying second-hand slate for the roof, and including whinstone they had excavated to build a retaining wall at the rear of the garden.
Although, at the time, Elaine reckoned that an air source heat pump might prove to be more expensive than gas to install and run, she took the view that, “because Scotframe’s Valutherm+ panel system provides such a well-insulated airtight building envelope, the need for as heating would be reduced. The difference between installing gas or the heat pump was covered by the renewable heat incentive, and now it may even be fractionally cheaper than using gas, so I’m very pleased,” she says.
Interior design
Downstairs the house has the triple aspect lounge at one end, with the kitchen/dining room at the other end next to the garden. There’s also a small utility room, bedroom and Jack and Jill bathroom. Upstairs are two further bedrooms and a bathroom, an office, and a boiler room.
The couple wanted the house to be fairly simple and contemporary with clean lines, with Elaine drawing inspiration from self-build shows and magazines.
Having been living in the house since April 2021, they love it. Highlighting her favourite feature, Elaine says the double height hallway “is the bit that everybody comes in and goes ‘wow’ at. They’re not expecting it because the house appears small from the outside – it’s a bit like a Tardis.”
Having created their ‘forever home,’ Elaine flatly refuses the idea of doing another one. “One is enough, it takes over your life,” she says. They finally received their completion certificate in April this year, another high point after all the challenges. “It was great to finally get it!” she says. “I still look at the house and can’t believe we’ve managed to fit all this in. We’re delighted.”
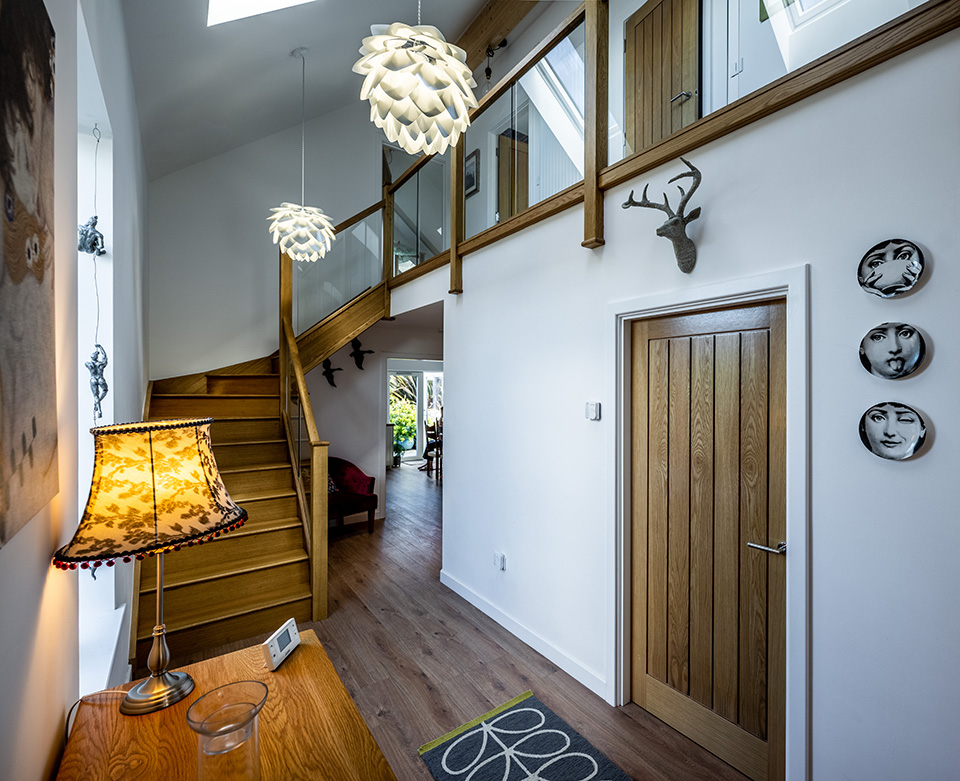
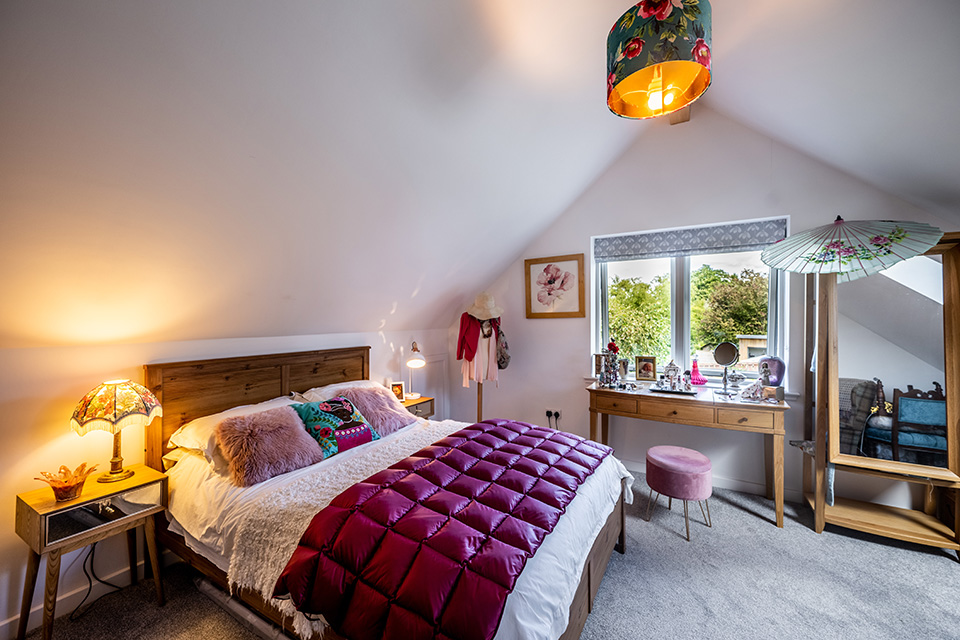
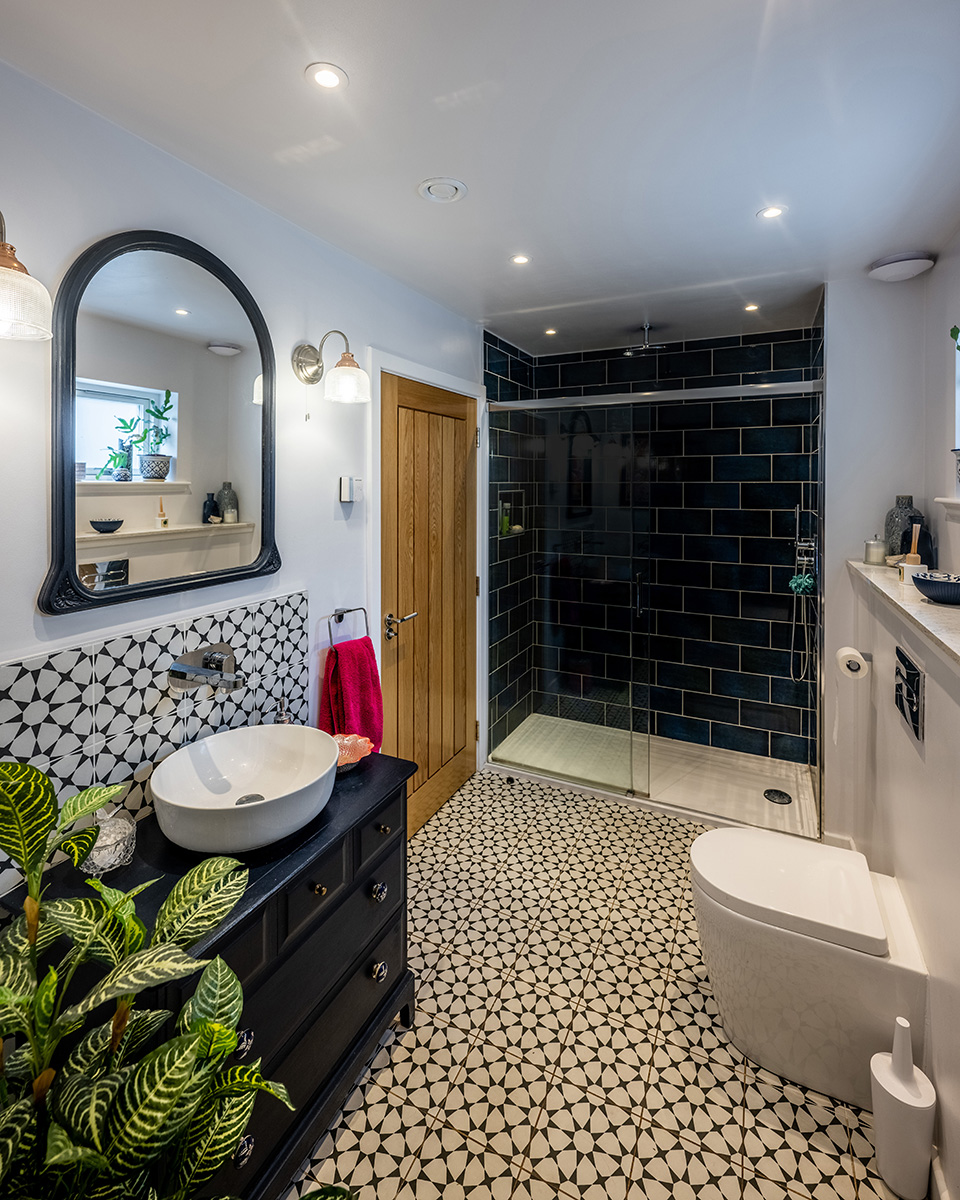
Tips for self-builders
- Where contractors were required, Elaine made sure she was always onsite, supervising and correcting if anything wasn’t being approached correctly.
- You have to be realistic – if you want to do something with a ‘DIY’ approach you have to have stamina, perseverance and the capacity for relentless hard work.
- Don’t assume that the professionals always have the best solutions.
Think through the consequences of any decisions. An example cited by Elaine was their pre-emptive attempt to placate the planners by putting the house in a lower part of the site than originally intended, but this meant that when they came to connect to the main drains the pipe missed the original connection point. “Fortunately we managed to pick it up at the far corner of the plot, but it meant getting rid of a lot more soil, a lot of pipework to do, and finding somebody to do the sewer work. That simple decision cost us about £5,000,” said Elaine.