A Grand Design of a Wedding Village to Match a Grand Old Stately Home
Ellingham Hall has all the timeless qualities that a country house should possess … grandeur, stateliness and an easy refinement. So when owners Aidan and Helen Ruff embarked on an ambitious project to build a small village of cottages in the grounds, he knew exactly the direction he wanted to go.
The result, which is taking shape in partnership with Scottish timber frame specialists Scotframe Timber Engineering and local artisans, is a development which seamlessly blends the best of modern building technology with the traditional craftsmanship of the English countryside.
Ellingham Hall, near historic Alnwick
Ellingham Hall is a beautiful building in sparsely populated surroundings near historic Alnwick in Northumberland. The hall is steeped in its own history, dating back to the baronies of Henry I. It was home to the Haggerston baronetcy, sheltered priests during the Reformation and survived two devastating fires. After the war, when Land Girls grew vegetables on the old tennis courts, it was used as a boarding school.
Aidan and his wife Helen took on the grand old residence when it had fallen into dereliction and spent 10 years painstakingly restoring it to its former glory. It now has a new lease of life as grand and highly-prized wedding venue.
And it was a procession of joyful and colourful marriage ceremonies which were the impetus for the Ruffs’ vision of a wedding village which would let even more people share in the bride’s big day.
While the Hall could provide luxury accommodation for 30 people, weddings attracted up to 120 guests. By building three detached cottages and eight semi-detached homes in rural Northumberland natural stone, the Ruffs are now able to offer unique and stylish quarters for all 120 visitors.
Aidan said: “We could have obtained planning permission for standard five-bedroom detached houses but we wanted to do something that was in keeping with the surrounding villages, so we created one and a half storey buildings which are derived from the built environment of the local area.”
Scotframe
Aidan got in touch with Scotframe after exhaustive research into methods of building the homes he wanted. Scotframe supplies to customers across the UK from its manufacturing facilities in Cumbernauld near Glasgow and Inverurie in Aberdeenshire and is recognized as being one of the industry leaders in timber engineering.
But what initially attracted the Ruffs to the Scotframe offering was the “completeness of the kit”.
The Kit
Aidan said: “The kits contained everything up to the roofing felt, including all the internals, even down to the last nail. It saved us an administrative nightmare trying to source all these elements ourselves.
“They weren’t the biggest company we considered and they weren’t the smallest. Some of the bigger firms didn’t even bother to get back to us with a quote and, with smaller companies, we were concerned about reliability of supply.
“Scotframe were responsive, attentive and competitively priced from day one. They even invited us up to their factory in Cumbernauld, near Glasgow and their sales, estimating and technical people were right on the ball. They showed an adaptability and flexibility – especially relating to differences between Scottish and English planning regulations – which really expedited our dealings with Berwick Council.”
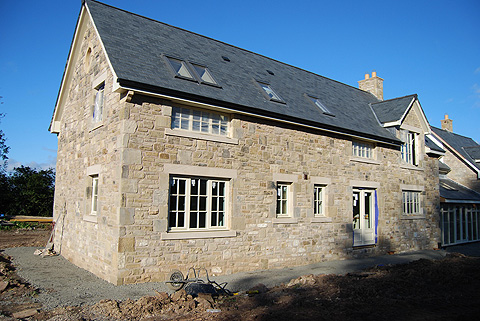
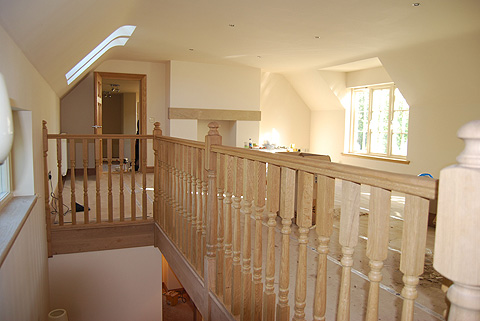
Dependable delivery
Dependable delivery was also an issue and here the company excelled. The orders for all the kits were placed in December last year and were on site by the third week in May. Even Aidan’s joinery team was impressed. After finding their way with the first of the kits, the joiners erected the next ones in half the time.
To make the cottages as authentic as possible, Aidan sourced reclaimed local stone and even took a large chunk of it into the council offices to get their approval. He has retained a team of local stonemasons, whose attention to detail is such that they look out for patches of lichen on the stones and incorporate them in the build. With the addition of stone lintels, cobles and original bulls-eye windows, many visitors have assumed the cottages are a restoration rather than a new build.
Aidan specified to Scotframe that all the internal finishes such as skirtings and architraves, should be solid oak. Doors are of composite construction with a heavy oak veneer so that “they shut with a soft clunk, like a Jaguar”.
Environmental standards
Scotframe’s strict adherence to environmental standards also smoothed the project’s passage through the council process and Aidan said that key elements such as thermal performance were well beyond required values “will save us a fortune”.
The dividends have started already. When Aidan had the cottages valued for insurance purposes, one was £85,000 and another £65,000 over what he had initially estimated the value to be. “It just goes to show,” he said, “people will always pay for quality.”